ADDITIVE MANUFACTURING

Additive
Manufacturing
(DfAM)
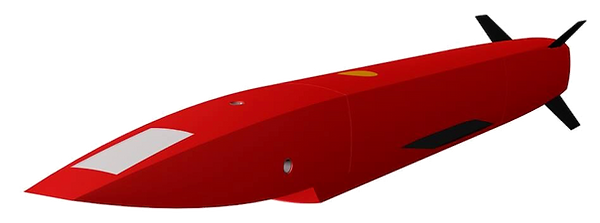

Additive Manufacturing for Missiles
Additive Manufacturing is seen as a key technology enabler for future missile systems
The potential of enhanced thermal management, innovative architectures and increased packaging densities to increase performance make Additive Manufacturing an attractive solution. The challenge is to demonstrate the capability to produce and qualify high performance parts with consistently high quality.
The MBDA-Huneed collaboration focuses on addressing these challenges using laser powder bed fusion of:
-
EOS Titanium Ti6Al4V alloy
-
ap&c Titanium Ti6Al4V alloy (astm f2924)
MBDA AMTDP Project Phase 1: Q1 2020 – Q4 2020
MBDA AMTDP Project Phase 2: Q1 2021 – Q4 2022+
MBDA AMTDP Project Phase 3: 2022+




Additive Manufacturing
for Military Aircraft
Huneed is the first Korean metal 3D printing company to be certified by KAl and ROKG
1ST Titanium Metal AM Application On Korean Military Aircraft
Additive Manufacturing project for producing fighter jet parts with Ti-64 for both First Article Inspection and Serial Production
Korea Aerospace Industries' indigenous fighter program KF-21

SEAL, GAS, GUN PORT
› Gas seal located at gun port that functions to seal hot
gasses to cycle the action as the gun operates
› Weight : 0.410 kg
› Operation Temperature: 226°F (108 °C)
› Manufacturing Time: 17hours (60μm)
AIR SCOOP VENTILATION GUN
› Air scoop located near gun port that
functions to ventilate gasses and
temperature cooling during while gun
operates
› Weight : 0.190 kg
› Operation Temperature : 215°F (101°C)
› Manufacturing Time: 2EA / 34hours (30 μm),
4EA / 46hours (30 μm)


DUCT, COOLING AIR SYSTEM, MANIFOLD
› Duct and manifold located at forward fuselage which is
connected to ECS system to feed cooling air to cockpit
› Weight : 0.580 kg
› Operation Temperature: 226°F (108°C)
› Manufacturing Time: 45hours (60 μm)